Posted on December 09, 2021
Cement production has more than doubled since the turn of the century. It now stands at more than 4.1 billion tons. Future growth could increase production another billion tons per year by 2050.
The concrete industry generates approximately 6-7% of global carbon emissions. Energy-intensive clinker production is a key factor. According to the Portland Cement Association, combustion accounts for about 40% of a cement plant’s emissions. Calcination accounts for the other 60%.
The latter is a process emitting CO2 as limestone and clay are heated to approximately 950 degrees Centigrade. Overall, production of a pound of cement releases about 0.9 lb of carbon dioxide. The carbon emissions of a cubic yard of concrete is about the same as the CO2 emitted by a full tank of gas in a typical passenger vehicle.
A life cycle assessment (LCA) provides a complete picture of the environmental impact of concrete. This is particularly true of exposed concrete, because carbonation occurs throughout its service life. The process actually absorbs CO2 from the air. Carbonation continues as concrete gets crushed at the end of its life cycle.
Low-carbon cement plants are key to increasing the industry’s sustainability.
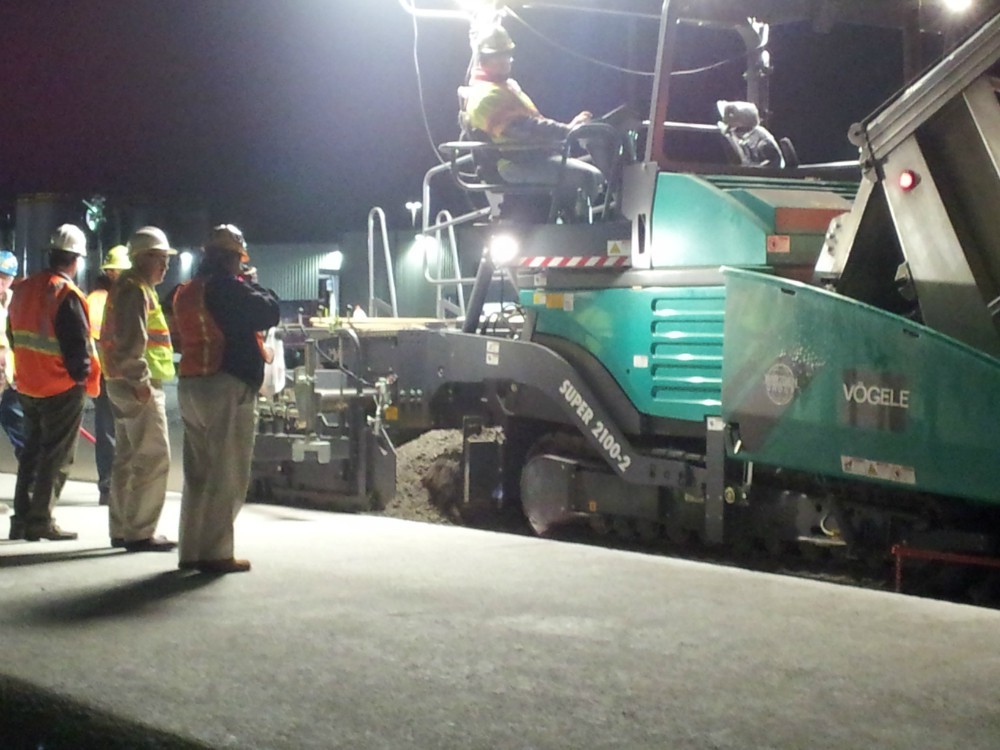
The Industry’s Quest for Carbon Neutrality
A key part of the quest for carbon neutrality involves the kilns at cement plants. There are two basic ways to address this. First, reduce the use of fossil fuels in the calcination process. Alternatives include bio-fuels and hydrogen. Green hydrogen acquired through the use of renewable energy sources is ideal.
Second, deploy effective carbon capture, utilization and storage (CCUS) technologies. Third, reduce cement consumption with innovative concrete mixes, like Portland-limestone cement (PLC). A plant upgrade planned for Sweden addresses the first two.
First Carbon Neutral Cement Plant
Heidelberg Cement's inaugural CCS project was at Norway’s Brevik cement plant. It was in fact the industry’s first full-scale installation for carbon capture. The system captures 400,000 tons of carbon dioxide per year. This is half of the plant’s estimated emissions from 2024 onward.
Now, Heidelberg intends to make its Slite plant in Gotland, Sweden, carbon neutral. A new carbon capture system will have a capacity of 1.8 million tons per year. This is more than four times the capacity of the system at Brevik, and equal to the plant’s total emissions. Heidelberg hopes to have the system operational at the plant by 2030. The company plans to store captured CO2 several kilometers down in bedrock.
Approximately 75% of Swedish concrete uses cement produced at the Slite plant. This means the project will have a significant impact.
Other Projects
At cement plants, CCUS is but one approach to increased sustainability. Reduced reliance on fossil fuels is another. Other plants are embracing new technologies to reduce their carbon footprint. Here are some examples.
Redding,CA, cement plant
Lehigh Hansen and Fortera will collaborate to make cement production less carbon intensive. Fortera's proprietary recarbonation process simply taps into existing systems. It captures carbon dioxide exhaust and cycles it back to the kiln.
The resulting supplementary cementitious material (SCM) is blended with ordinary Portland cement (OPC). It can also be used as a 100% cementitious binder in preformed products like bricks and blocks. The manufacturer expects the new system will reduce emissions by 60%. The project will demonstrate the quality, scalability and economic viability of Fortera’s technology.
Rillito, AZ, cement plant
CalPortland’s cement plant in Rillito, AZ, is the recipient of the EPA’s 2020 Energy Star certification. The plant has received the certification every year since 2012. A plant's energy-efficiency must be in the top 25% nationwide to qualify.
Recent energy-saving efforts include:
Replace two preheater tower cyclones
Upgrade a quarry belt conveyor with 11 km of new belting
replacing the kiln baghouse fan and dust collector bags
The human element is also an ongoing consideration. The plant gets an expanded energy team, and they attend more energy meetings. Efforts to communicate energy best practices to plant personnel will intensify. A 2.5-minute video from CalPortland provides perspective on the industry’s pursuit of sustainability.
Florence, CO, cement plant
The Denver Post reports on a carbon-capture facility planned for a LafargeHolcim plant in Florence, CO. The Department of Energy contributed a $1.5 million grant. The CCUS project will sequester CO2 underground. Svante will develop the CCUS system. Potential annual carbon capture is estimated at 725,000 tons.
Svante shares its name with Svante Arrhenius, a Nobel Laureate in Chemistry that saw the potential for fossil fuel combustion to generate a greenhouse effect. The Canadian company captures CO2 from industrial sources at half the cost of competing technologies. Its approach relies on solid adsorbents rather than traditional liquid solvents. Tailor-made nano-materials catch and release carbon dioxide in less than a minute. Capacity is impressive. A piece of the material the size of a sugar cube has the surface area of a football field.
Victorville, CA, cement plant
In February, 2021, Cemex USA announced it received a grant from the Department of Energy to develop carbon capture processes at its Victorville, CA, plant. It will partner with RTI International, Oak Ridge National Laboratory and Carbon Clean. In August, 2021, Cemex announced an $8 million investment in UK-based Carbon Clean. It will deploy next-generation non-aqueous solvents to enhance the efficiency of the system.
About PACA
The Pennsylvania Aggregates and Concrete Association (PACA) reports on developments and innovations in the concrete industry. Our team welcomes your inquiries about concrete and sustainability. Please contact us with your questions.