Posted on February 28, 2019
Construction aggregate includes a range of particulate materials - ranging from coarse to medium grains - including sand, gravel, slag, crushed stones, and recycled concrete. These materials are mixed in with concrete to give the end product a strong and durable finish.
Construction contractors and customers alike, look for affordability and strength above all else. A world of difference can be seen in both these factors when the right concrete aggregate is utilized. One viable aggregate that comes in multiple sizes and scales is hardened concrete.
As buildings, roads, bridges, and other structures are demolished every year, hundreds of thousands of tons of debris is generated. As the world moves towards saving the environment, and governments offer tax rebates to those investing in fuel-efficient technologies in an effort to reduce their carbon footprint; recycling this debris is the perfect way for any contractor to save the environment and their expenses, all while ensuring strength in the foundation of their new structures.
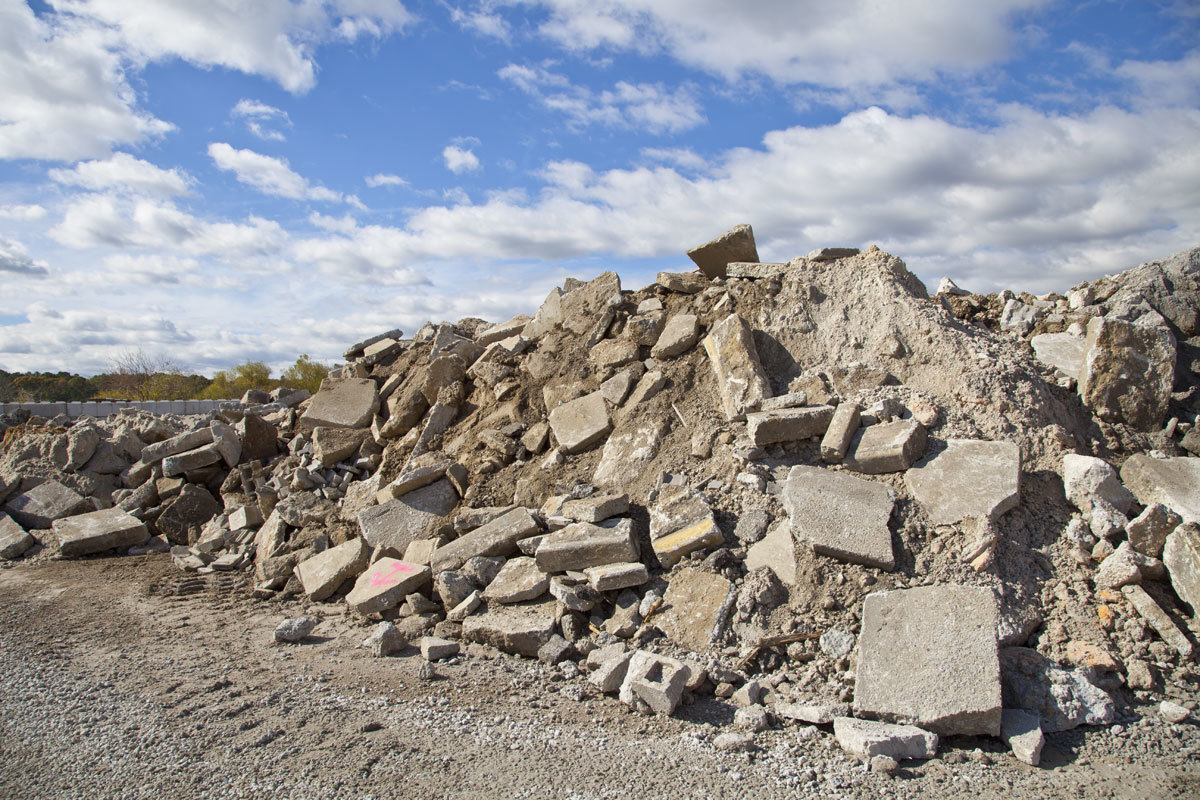
Why Is Aggregate Used?
The purpose of aggregate is to increase the volume of a concrete mix while ensuring minimum air is trapped within the structures. The material that makes up the aggregate is of different shapes and sizes, allowing them to fit snugly with one another.
The larger, coarser aggregate particles settle together to constitute a skeletal structure for the mixture. Smaller particles serve as fillers between the spaces between these larger particles, and in turn particles even smaller rush to fit into the gaps between the fillers.
Finally, the smallest gaps within the aggregate are filled with cement particles, holding the whole structure together. This property shows that the better the size distribution provided in aggregate, the stronger a concrete structure will be; however, it is necessary to keep in mind the optimum amount of recycled aggregate that should be added to the concrete mix. Changes in the blend can lead to an overall decrease in the strength of your structure, which is why recycled aggregate remains most appropriate for bases and sub bases.
Recycling Concrete Aggregate
History
Crushed concrete has been in use since the ancient times, only to be integrated with gravel, sand, and cement to ensure durability. The practice was first recorded in the 1860s. US construction companies were reluctant to use the technique at first, since crushing cured concrete proved to be much more cost-intensive in terms of labor.
However, in the 1970s, when the construction era was at its peak, landfills refused to accept broken concrete, since it had no recyclability, and took up too much space. One landfill, on the other hand, continued accepting concrete dumps, crushing it with the help of bulldozers and rollers, and reselling it as aggregate.
After a number of successful projects, construction companies confirmed that not only did recycled concrete offer equal durability and strength in new concrete; it also had a much lower impact on the environment.
With advancements in construction technology, recycled concrete aggregate has seen further developments, making it much more refined and cost-effective.
How It's Done
Thanks to increased environmental laws, and the desire to keep construction costs down, recycled concrete aggregate has found quite a following. Due to its assimilated nature, it provides even higher economies of scale then those possible with the use of regular aggregates.
Demolished concrete is collected from sites and put through crushing machines. These machines can reduce larger rocks to smaller rocks, gravel, or even dust! The concrete can be refined for rebar, wood, or other metal chunks before being added to these machines. There are several types of crushers:
- Jaw crushers
- Gyratory crushers
- Cone crushers
- Compound crushers
- Horizontal and Vertical shaft impactors
- Mineral sizers
- Crusher buckets
Most of these crushers use an impact force, or a ‘tumbling’ mechanism to break down larger stones.
Strength & Durability of Recycled Aggregate
The water absorption value – or penetrability – of recycled aggregate is 7.5%, much higher than the minimum (3.7%) required by the Washington State Department of Transportation’s (WSDOT) construction division. This higher rate is attributable to gravel’s own absorption rate, added to that of the paste.
Different portions of the recycled aggregate hold varying measures of specific gravity, characterizing the cured cast’s strength, compression-resistance, and modulus elasticity. However, using a recycled aggregate of more than 65% can impact the mix’s durability significantly, reducing its physical properties tenfold. The optimum amount blended in with the concrete should be 35%.
Some experiments have shown that the recycled aggregate is durable, no doubt, but not as sturdy as natural coarse aggregate. However, to tackle the lack of strength, you can treat the mix with materials such as fly ash.
Benefits
Recycled concrete aggregate presents numerous benefits:
- Increased protection from seepage
- Reduced costs, since it doesn’t need to be mined
- Reduced environmental impact, more appealing to governments and customers
- Preserves natural resources such as gravel, water, coal, and oil
- Reduced space wastage in landfills
Disadvantages/Risks
As with everything, the aggregate also presents certain risks that constructors should be aware of:
- If a high concentration of aggregate is used, the structural integrity of the casts fail, leading to cracks and numerous faults within the structure.
- The aggregate must be refined. Otherwise it could lead to various challenges. A prime example of that is the use of recycled concrete for Highway 427. The presence of deleterious materials, i.e., gypsum, wallboard, drywall, and plaster found in the final cast were due to unrefined concrete aggregate, leading to cracks in between lanes, as well as an uneven road surface.
- Brittle concrete might be mixed within the aggregate, leading to uneven grading.
- Supplements need to be added to make the final cast as strong as it can be with natural aggregate.
- Visual inspection is necessary to ensure the mix is refined.
Recycled concrete aggregate offers many diverse advantages, among the most prominent are safety and durability. However, keeping in mind the complications posed by the use of concrete aggregate in overlays, it is highly advised to utilize recycled concrete for bases and sub bases.
If you are looking for a sustainable solution for your construction needs, you don’t need to look any further than Specify Concrete, a safe and reliable construction company brought to you by the Pennsylvania Aggregates and Concrete Association (PACA).