Posted on September 30, 2021
Calcination accounts for a significant percentage of concrete’s total carbon footprint. According to the Global Carbon Project, heating up limestone accounts for about four percent of global CO2 emissions.
In early 2021, Northwestern University researchers released a comprehensive carbon reduction plan. It seeks net-zero emissions for the concrete industry by 2050.
The team conducted a cradle-to-cradle analysis of the full cement/concrete cycle. They highlight the need for more efficient kilns and the increased use of biogenic fuel. They also look at the potential of newer technologies involving:
Carbon capture and utilization
Greener cement chemistry
Materials efficiency
The plan suggests ways to speed up the pace of innovation. It also looks at government policies that promote net-zero concrete.
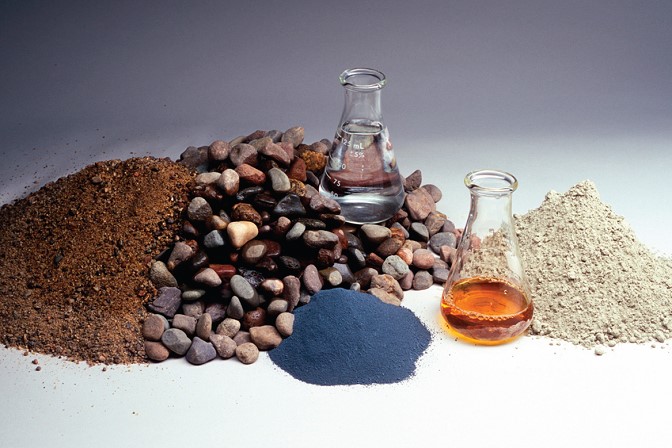
Portland Limestone Cement: A Brief History
Portland limestone cement (PLC) remains an important way to reduce concrete’s carbon footprint. PLC is not new. It's been a proven product in Europe for more than 50 years. It is newer in the United States. It first appeared in a 2007 paving project in Colorado.
Cement with 20 percent limestone appeared in Germany in 1965. In 1992, the UK updated standards to allow for the same concentration. Today, European standards exist that allow concentrations of up to 35 percent limestone.
Given the above, untapped potential remains. Acceptance by more state DoTs would also help. At present, 34 states allow PLC for transportation projects.
PLC reduces emissions by up to 10 percent without compromising performance. Contractors use PLC in pavements and bridges. They also use it in government buildings, residences, schools, hotels and parking garages.
The year 2012 saw updates in blended cement spec ASTM C595. It covers two types of PLC cement:
Type IL: Portland-Limestone Cement that is 5-15 percent limestone (by mass)
Type IT: Ternary Blended Cements combining PC, pozzolan, limestone slag cement and limestone
For the period 2012-2016, United States PLC production exceeded two million tons.
Calcination, a high-temperature transformation of limestone in kilns, is energy-intensive. It accounts for 60-65 percent of all the energy consumed in cement production. Combustion & grinding accounts for the remaining 35-40 percent.
Calcination also accounts for 60 percent of CO2 emissions associated with cement manufacturing. Every ton of clinker produced by traditional means releases 525 kg of CO2. Any reduction in the amount of Portland cement used in a concrete mix cuts CO2 emissions. Adding finely milled limestone allows just that.
Increased hydration efficiency
Better yet, the limestone added to the mix also delivers increased strength. Since limestone is softer than clinker, it grinds finer during milling. This results in a denser paste that requires less water. More fine particles increases the total surface area on which cement hydrates form. This frees up clinker grains for extra hydration. The result? Small, yet notable improvements in performance.
PLC offers other advantages. PLC delivers improved pumpability and finishing. Increased surface areas reduce bleeding.
Updated Environmental Product Declarations (EPDs)
New Industry-Wide Environment Product Declarations (IW-EPDs) arrived in April 2021. They apply to Portland Cement (PC) and Portland-Limestone Cement (PLC). The IW-EPDs profile material, fuel and energy factors regarding concrete’s key ingredients. The documents help ready-mix producers with marketing and compliance. To compile the IW-EPDs, PCA considered guidelines from to key sources. One is the Global Cement and Concrete Association. The other is the International Organization for Standardization.
The new PC EPD updates the 2016 version, while the PLC EPD debuts in 2021. The new IW-EPDs are valid for the period 2021 to 2026. The PLC EPD cites greenhouse gas (GHG) figures for blended cements with 5-15 percent milled limestone.
The new IW-EPD draws from data generated by a significant sampling of PCA producer members.
The SCM tested was two-thirds slag cement and one-third fly ash. Early strength declined in both PC and PLC. However, both 28 and 56-day strengths rose to the 40-percent level. The rapid chloride permeability test revealed that both PC and PLC have lower permeability when cured longer and when using SCMs. Both exhibit similar trends. The data reveals that, compared to 2016, GHG emissions for PC decreased 11.3 percent. And, PLC’s carbon footprint comes in at 8.2 percent less than that of traditional Portland cement.
PLC Case Studies
Contractors use PC and PLC in applications calling for Type I and other general-use blended cements. PLC in use at prominent projects across North America.
Daytona Beach Convention Center - Florida
Contractors used PLC to construct the North and South Towers at the Daytona Beach Convention Center. Specified design strengths ranged from 2,500 to 14,000 psi. The 31-story North Tower required 40, 324 cubic yards of concrete. The South Tower required 35,607. PLC performed as needed during two mass pours of 7,722 and 6,003 cubic yards.
Tim Hortons Field - Ontario
Another example is Tim Hortons Field in Hamilton, Ontario. About 30 mixes went into a total of 14,000 cubic yards placed. The contractor mostly used Portland-limestone cement for exterior applications. Designers specified strengths to 5000 psi. The project went smoothly despite significant cold weather construction. The sports stadium qualified for LEED Silver certification.
Pueblo County Health Department - Colorado
Contractors also used PLC during construction of the Pueblo County Health Department. The piers, interior floors, curb and sidewalk all consist of PLC. Mixes included 25 percent Class F fly ash. Designers specified 3000 psi for the interior floors. The 28-day field average was 4320 psi. The curb and sidewalk spec was 4500 psi. The 28-day field average was 5660 psi. Finally, the pier specification was 3000 psi. The 28-day field average was 4510 psi.
Eighty percent of states approve PLC projects. Most exceptions are in New England and the Southwest U.S.
Cement producers continue to come up with new PLC formulations. For example, Lehigh Hanson launched EcoCem Plus for Canada’s Prairie Market. It is a blended PLC combining inter-grinding clinker, fly ash, limestone and gypsum. EcoCemPlus delivers strength and durability while reducing the carbon footprint.
About PACA
The Pennsylvania Aggregates and Concrete Association (PACA) reports industry news at SpecifyConcrete.org. If you have questions, please don’t hesitate to contact us.