Posted on September 02, 2021
Concrete industry professionals improve energy efficiency, maintain quality and reduce carbon emissions. The use of sensors, artificial intelligence (AI) and data science help in all three areas.
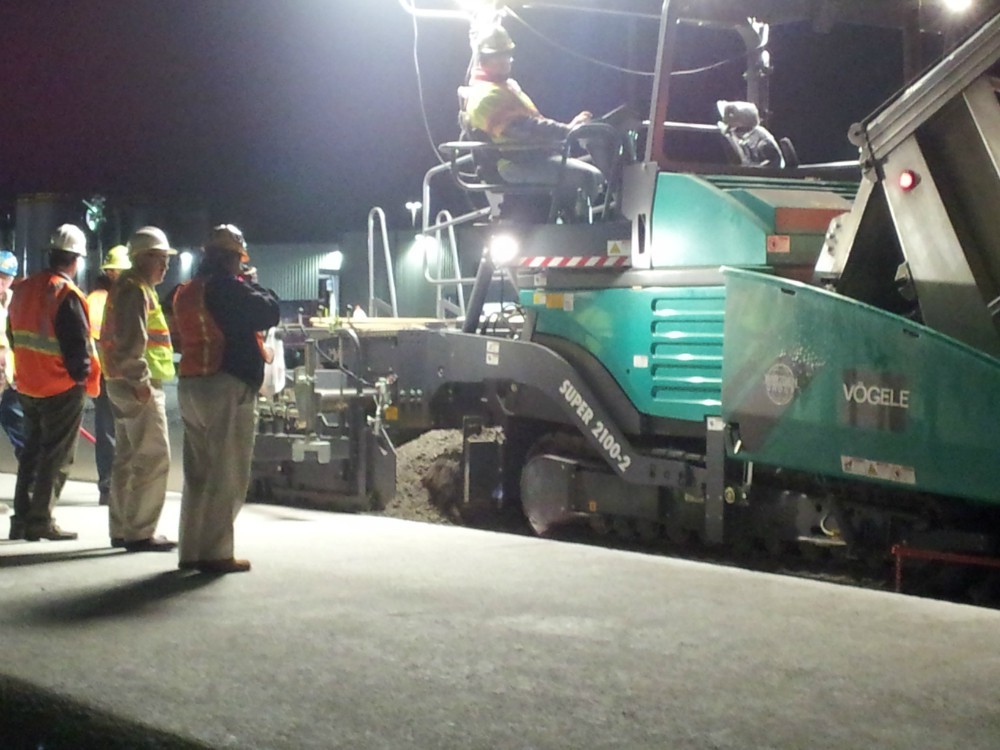
Sensors and Smartphone Monitoring
Contractors have used traditional sensors for years. Concrete mixes are still subject to a month’s worth of testing in the lab. A maturity curve graphs concrete strength over time. Contractors compare in-lab and field results to determine when the concrete is strong enough.
Weather or other factors may require time-consuming changes in the approved concrete mix. The new mix requires the graphing of a new maturity curve.
A new generation of concrete sensors provide:
Quick insights into temperature, maturity, and strength.
A way to fast-track project timelines.
Opportunity to use real-time data to enhance efficiency and productivity.
Consider LumiCon wireless concrete sensors for example. They allow real-time monitoring of temperature, strength and maturity. They also measure relative humidity, evaporation rate and temperature differential. They replace traditional single-point sensing with Cloud-based technology. The system provides real-time remote access to information. It is also possible to run reports and share data with stakeholders. Real-time weather data allows contractors to monitor weather’s impact on projects underway.
Building Sensors
New sensors developed at Purdue University also end much of the traditional off-site testing.
Concrete floors are common in multi-story buildings. It is critical to determine when a floor can take on loads so construction above that floor can proceed. Purdue’s plug-and-play sensors allow direct measurement of the strength of a concrete floor deck in real time. The sensors use electricity to send an acoustic wave through the concrete. A wave propagating through concrete details strength and micro-structure. The sensors deliver better data-driven decisions to improve quality and accelerate construction timelines.
For example, researchers embedded twelve sensors in the third floor of Purdue's new Gateway Complex. Real-time data allowed for on-the-fly decisions.
Highway Sensors
Embedded highway sensors save contractors time, money and onsite labor. They also reduce risk and improve construction safety. They help determine when new pavement can handle traffic. Monitoring of freshly placed pavement patches reveal when they can handle heavy trucks.
Traditional maturity and flexural-strength testing were limiting. In the past, engineers erred on the side of caution due to the risk of curling and warping. With embedded sensors, contractors know exactly when the required maturity occurs. Monitoring data from embedded sensors eliminates the need for repeated re-calibration of mixes.
The sensor developed by Purdue researchers “lives” in the concrete. Each one monitors an 11-inch section of concrete. Piezoelectric sensors tied to rebar directly measure electrical data. It is possible to analyze data hourly if desired. This can prevent exposing fresh concrete to traffic too soon.
Sensor-enabled data science can save millions of dollars in construction costs. They also improve construction safety by limiting lane closures.
Sensors and Long-Term Monitoring
Permanently embedded highways sensors provide stakeholders with timely data on emerging concrete distress. In a collaboration with INDoT, Purdue researchers put sensors in interstate highways near Indianapolis. The team from Purdue is also working with the Federal Highway Administration to expand into other states. Missouri, Kansas, Texas and California all plan to take part. View a YouTube video here.
AI and Data Science in the Industry
A combination of well-placed sensors and AI is key to improved industrial processes.
AI reduces performance volatility at cement plants
Performance volatility is a common concern at cement plants. Throughput and energy usage may deviate as much as 50 percent from average. This occurs because existing automation and control systems have “have reached their limits.” Inherently unstable processes remain a problem.
In 2019, McKinsey reported the results of a study that analysed AI's effectiveness. The research occurred at a North American cement kiln and mill.
Deep learning algorithms, machine learning, and neural networks delivered real-time optimization. The results were impressive. AI improved both throughput and energy-efficiency by up to 10 percent.
The use of AI:
Cut CO2 emissions
Reduced energy consumption
Increased profits
AI at Solidia
Solidia is a company working on next-gen, low-carbon concrete manufacturing. Its patented cement manufacturing and concrete curing technologies reduce carbon footprints. The New Jersey-based company estimates its technologies offer potential annual savings/reductions of:
1.5 Gigatons of COâ‚‚
3 trillion liters of fresh water (concrete curing tech)
Energy consumption equivalent to 67 million tons of coal
100 million tons of concrete waste landfill
Sensors are key to Solidia’s systems. Sensors put “eyes inside the curing chamber that can expedite production upgrades and efficiencies, new recipes, and improved performance in concrete.” Solidia employs AI to deliver an intelligent concrete curing process. This improves quality control and reduces waste.
Solidia Cement is manufactured at lower temperatures than OPC. This reduces a cement kiln’s carbon emissions. Solidia's AI-empowered curing process sequesters CO2 while strengthening the concrete. Solidia’s concrete cures in a fraction of the 28-day time required for OPC.
Solidia uses extensive data collection to speed the development of better concrete formulations. This will help mitigate carbon taxes as more stringent CO2 regulations arrive.
AI at Heliogen
Heliogen is a company harnessing the power of sunlight to replace fossil fuels. HelioHeat is a concentrated solar power (CSP) technology. It generates the ultra-high temperatures needed to power heavy industrial processes. Examples include cement, mining, petrochemicals, waste treatment and steel.
The company uses AI to fine-tune the movement of the thousands of mirrors. Synchronized mirrors help generate the extreme heat needed to turn limestone into clinker. This reduces the need for fossil fuels responsible for much of the industry's carbon emissions.
About PACA
The Pennsylvania Aggregates and Concrete Association (PACA) reports on the latest developments in the concrete industry. SpecifyConcrete.org informs both the public and those in the industry. For further assistance, please contact us.