Posted on May 28, 2020
Net-zero is the gold standard in green construction. The term “net-zero” says it all. A net-zero structure uses less energy than it generates. It combines energy-efficient construction with on-site renewable energy. Solar, passive solar, wind and geothermal are common energy sources.
ICFs contribute high R-values, thermal mass and continuous insulation to net-zero designs. Energy efficiency is important today and likely even more important in the future. For example, Pennsylvania's residential rate of 12.75 cents/KwH ranks it 16th in the nation. Today more than ever, the home is a sanctuary. With ICF construction, it’s a quiet one as well. ICFs reduce street noise and the sounds common on windy days. ICFs are also storm, fire, insect-resistant.
Builders embrace net-zero construction because it’s more cost-effective than ever. Although ICFs are most commonly fabricated from expanded polystyrene (EPS). Some consist of extruded polystyrene (XPS) or recycled polystyrene. Standard ICFs are usually rated around R-22. Additive ICF systems offer up to R-40 insulation, a real plus in net-zero construction. To better visualize the ICF construction process, check out this time-lapse video from the Insulated Concrete Forms Manufacturers Association (ICFMA).
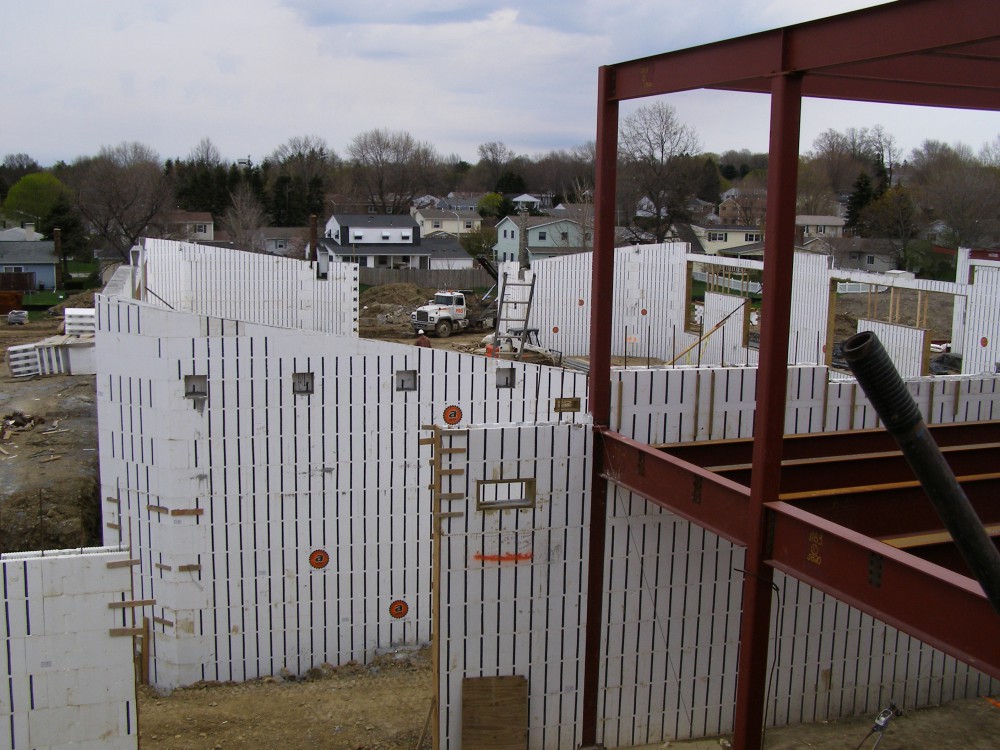
ICFs: Superior for Net-Zero Construction
Net-zero structures built with ICFs already deliver energy savings in the state. For example, the Lombardo Welcome Center at Millersville University is an early example of net-zero success. In its first year, the $10 million Lancaster County building generated 75 percent more energy than it required. The ambitious design includes 500 rooftop solar panels and 20 geothermal wells. It saves the university an estimated $5,000 per month in energy costs. The International Living Future Institute has certified more than 100 projects. The Lombardo Welcome Center ranks third.
Quadlock details “Five Steps to a Successful Zero Energy House.” Part of the process is to take advantage of concrete’s thermal mass. The post declares unequivocally, “Build exterior walls and floors with concrete.” The thermal mass of concrete reduces seasonal temperature swings. It transmits relatively constant ground temperatures through the footings and into the home.
Fox Blocks ICFs are also used in net-zero designs. Energy savings can exceed 50 percent. Their ICFs feature core widths of four to 12 inches, and form widths of 9.25 to 17.25 inches. Ship-flat designs reduce transportation costs. BioFriendlyPlanet concludes that “ICF construction is by far the most superior technique.” Continuous insulation on both sides of the form eliminates thermal bridging. ICFs also deliver the airtight construction that’s so crucial to net-zero structures. A CLEB Laboratories study compared two whole wall construction techniques. One used standard 2x6 studs while the other used ICF forms. The latter delivered energy savings of 58 percent.
Case Studies of Net-Zero Homes
Net-zero residential construction runs the gamut from modest to upscale, to which these case studies will attest.
First in the Northeast
Talk about happy accidents. New York builder Anthony Aebi simply wanted to build a more energy-efficient home. Aebi built his first zero-energy home "when his search for a better building material led to insulated concrete forms (ICFs).”
After Aebi completed the 3,912 sq ft Gardiner, NY, home, he brought a tester to the site. Aebi learned that he “accidentally” built the first net-zero home in the Northeast. Projected energy savings are $228,000 over the life of a 30-year mortgage.
The crew poured the basement slab over 4.3 inches of closed-cell spray foam rated at R-27. ICF blocks extend from the slab to the roof. Sealed seams contribute to a drainage plane that eliminates housewrap. Steel reinforcement of the R-22 ICF walls adds to the home’s storm resistance. They also make it earthquake-resistant. An elastomeric door and window flashing delivers airtight, waterproof protection. LED lighting is used exclusively throughout the residence.
The home is remarkably airtight. Testing reveals an 0.12 ACH 50 which compares well to the Passive House Institute standard of 0.60 ACH 50.
Eagle Rising
Golden Eagles nesting on the site of a Colorado home inspired the name “Eagle Rising.” Storm resistance and sound attenuation were crucial requirements at the windy, hilltop site. ICFs were the perfect architectural and engineering solution.
High R-values, airtight construction and thermal mass contribute to coveted net-zero performance. So does radiant heat, passive solar heating and solar shading. ICF Builder named the project “Best Custom Home.”
Homes Under $100k
Deltec Homes is a company headquartered in Asheville, NC. Deltec disproves the idea that net-zero ICF construction is only for upscale residences. It offers a series of cost-effective designs priced from less than $100k. Deltec delivers LEED-certified homes that are more affordable than their non-LEED counterparts.
ICFs for ROI
Value retention and energy savings both drive return-on-investment (ROI). ICF net-zero construction often requires higher materials costs upfront. However, that expense is offset to a degree by reduced labor costs. Owners pour less money into labor and more into tangible assets. Current owners and future buyers all value the low-maintenance durability of ICF construction. Maximize benefits for all parties with third-party certification. It is important for builders and buyers alike. Constructing homes to net-zero standards is good business. Builders with net-zero expertise garner attention from environmentally conscious homebuyers. “Zero energy” and “zero energy-ready” certification assures homebuyers that they are getting what they pay for.
Learn More
The Pennsylvania Aggregates and Concrete Association (PACA) maintains the SpecifyConcrete.org website. The association serves a diverse constituency that includes contractors, suppliers and others. SpecifyConcrete.org delivers emerging information about industry innovations. For further assistance, please contact us.