Posted on June 25, 2020
On September 14, 2014, 60 firefighters arrived at the University of Nottingham to find a cross-laminated timber (CLT) structure engulfed in flames. The fire consumed a $24 million laboratory building that was about 70 percent complete. The likely culprit was an electrical short in a temporary power supply. The absence of windows and doors ventilated the fire to dire effect.
Following the devastation, the Chief Fire Officer of the Nottingham Fire & Rescue Service filed a report. He discussed how CLT buildings “are vulnerable from fire during the construction phase.”
The threat of fire during construction is but one of the challenges faced by CLT designs.
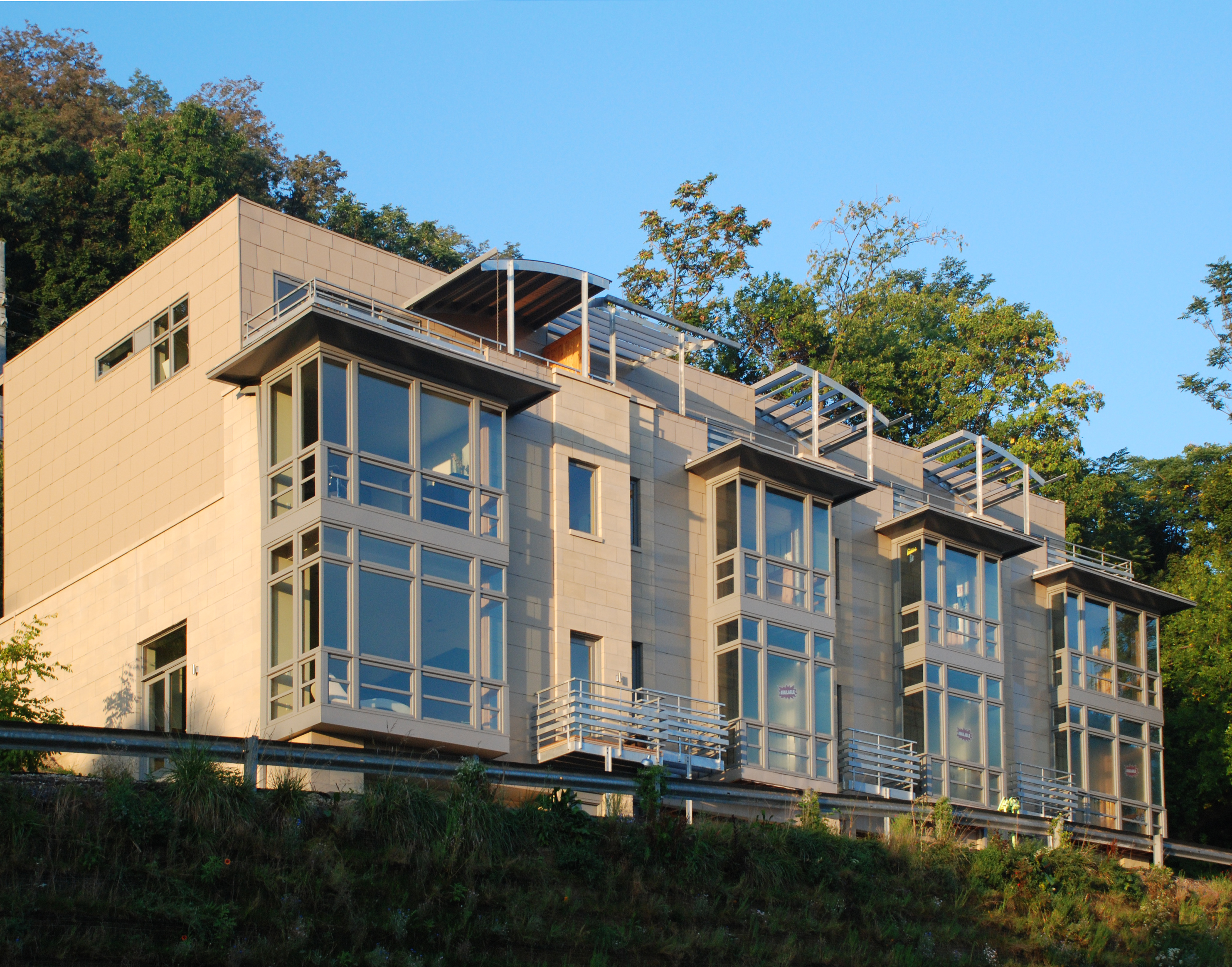
Concrete & Fire Safety: A Solid History
By contrast, concrete construction enjoys a long history of safety during the construction phase and beyond. This is reflected in the insurance premiums paid for both builder’s risk and property insurance. In a comparison of multi-family projects in Edgewater, NJ, builder’s risk insurance was 66.5 percent cheaper with concrete construction. Property insurance premiums were 57.7 percent lower.
Consider the fire resistance of insulated concrete forms (ICFs). Take Fox Blocks as an example. Their four-inch blocks have a two-hour fire-resistance rating (FRR). It is four hours for their six-inch blocks. ICFs also feature a low flame spread index (FSI) of 25, well below the code limit of 75.
Encapsulation in ⅝” gypsum board improves fire resistance. Accordingly, fire authorities tend to promote prompt encapsulation as tall timber projects proceed. At the same time, designers often want to leave CLTs exposed for aesthetic reasons. Even with encapsulation, there are limits. Gypsum-covered CLT can decay with a modest amount of fire exposure.
CLTs and Builder’s Risk
During construction, CLT builders cope with risks not experienced by concrete builders. In addition to fire risks, weathering is another challenge. In fact, weathering and moisture is such a concern that contractors often erect large tents to help protect the wood from the elements.
Over the years, cement and concrete have been the subject of widespread fire testing. For example, concrete’s resilience in the presence of a building fire has been the subject of research at MIT’s Concrete Sustainability Hub. By contrast, CLT construction is new enough that fire research is less comprehensive than that for concrete.
CLTs and Fire Studies
The common claim is that charring during a fire helps to protect a CLT beam’s structural integrity. As a post by reinsurance specialist AXA XL notes, “This is not an open and shut case, however, and the discussion around this topic continues.”
Any focus on the fire resistance of the mass timber alone may be misleading. One study suggests that “System properties are shown to be more significant. Delamination and encapsulation failure are critical to predicting the fire performance of timber.” The study goes on to state that “little research is available on these phenomena.
To further reduce fire risk, many architects specify an added step - the encapsulation of the CLT beams. However, consider the view expressed in an American Wood Council paper. It cautions that, “Potential failure of the encapsulation, however, can lead to the involvement of the timber in a fire and can eventually lead to a second flash-over.”
Another tall timber fire study concludes with a call for more dialogue among the experts. “The specific risks posed by timber structures necessitate a common dialogue between fire scientists and engineers.”
After the Fire: CLT Testing and Repairs
Any time a fire ravages a building, structural analysis follows. Weakened components require repair or reconstruction. Such analysis tends to be more complicated with CLT construction than with concrete and steel construction.
A representative from Chubb Insurance spoke on “CLT and Builder’s Risk” at a meeting of The Inland Marine Underwriter Association (IMUA). In the aftermath of a fire, assessing damage to concrete and steel is reasonably straightforward. Once structural integrity is confirmed, such materials can be “cleaned, painted and returned to service.”
But what about CLT members exposed to fire? Is structural integrity harder to assess? What is the future heat performance of CLT adhesives after a fire? Charred wood raises aesthetic concerns as well. In many instances, stakeholders will demand new CLT beams to play it safe and to address aesthetic concerns.
CLTs and Sustainability
In 2016, the ICC Ad Hoc Committee on Tall Wood Buildings proposed updated code requirements that apply to mass timber structures. The 2021 International Building Code (IBC) will allow for 18-story tall timber construction.
This only increases questions about sustainability. For example, construction of an 18-story CLT building requires an estimated 17 acres of forested land. In general, the proliferation of CLT construction increases deforestation concerns. By comparison, concrete’s components are both inert and plentiful.
The fact that wood stores carbon is often cited as a benefit of tall timber construction. But, three factors reduce this benefit by about 85 percent. Throughout the CLT production process, Carbon is released into the air due to:
- The rotting of logging residue
- Milling operations
- Product transportation
By comparison, as the concrete industry innovates, recyclable content expands. Fly ash replaces up to 35 percent of the cement in certain concrete mixes. According to the Green Education Foundation, each pound of fly ash used eliminates one pound of carbon emissions. Recycled aggregates are another example. The Portland Cement Association notes that “The LEED Green Building Rating System recognizes recycled aggregates in its point system.” Blast furnace slag, crushed glass and street sweepings further increase the total recycled content in various concrete mixes.
Learn More
The Pennsylvania Aggregates and Concrete Association (PACA) disseminates information about concrete construction. For additional information on CLTs vs. concrete, please contact us.