Posted on June 09, 2022
According to McKinsey, global construction accounts for about a quarter of greenhouse gas (GHG) emissions. Concrete is a significant contributor. It accounts for 4.5 percent of global GHG emissions and 7.0 percent of COâ‚‚ emissions.
As McKinsey’s December 2021 report states, “Decarbonizing the cement and concrete industry …. will play a pivotal role in addressing the climate challenge.”
The International Energy Agency (IEA) compares 2050 carbon neutrality goals and industry performance. It asserts that most heavy industries are not yet on track. The IEA says that the “direct CO2 intensity of cement production increased 1.8% per year during 2015-2020.” To achieve the proper pace, the industry needs annual reductions of 3.0% through 2030.
The IEA suggests a “sharper focus” on:
Reducing the clinker-to-cement ratio
Increasing the use of blended cements
Embracing innovative technologies like CCUS
The IEA also believes that governments should stimulate investment and innovation. They can achieve this through more R&D funding. Mandatory CO2 emissions reductions are another possibility.
Toward Greener Cement
While the reduced use of fossil fuels is a key goal, consuming less water is another. Water use is a heightened concern during prolonged drought. This is the current predicament in the western third of the United States.
One way to decrease cement’s carbon emissions is to reduce the need for calcined limestone. Here are three potential substitutes.
Milled limestone
Replacing up to 15% of the Portland cement with milled limestone is a prime example. This reduces carbon emissions by about 10%. Multiple studies establish that Portland limestone cement (PLC) performs as well as ordinary Portland cement (OPC).
Belterra clay
Belterra clay can serve as a partial (50-60%) substitute for limestone in the kiln. It contains aluminum compounds, making it an excellent raw material for making cement.
This idea is popular where there are good supplies of the substance. Traditionally, Belterra clay is a worthless byproduct of bauxite (aluminum) mining. Mining companies have to strip away as much as a hundred feet of the material before reaching the bauxite. Using once worthless overburden in cement production is very appealing. Although Bauxite itself is an alternative, it is far more valuable as a source ore for aluminum.
Also, it is possible to bake Belterra clay at 200 degrees lower than standard calcination temperatures. This means fewer emissions per unit of cement. Lab tests confirm that the Belterra clay formulation performs to OPC standards.
Volcanic rock
Stanford University researchers see volcanic rock as a replacement for limestone. Clinker production still requires very high kiln temperatures. However, there’s no CO2 released during calcination.
Volcanic rock clinker mixes with hot water to form complex molecular chains. This increases ductility while reducing permeability. The inspiration for the idea comes from the Romans’ marine concrete of two millennia ago. Back then, volcanic rock and seawater combined to form structures that still exist. In some applications, the formulation minimizes the need for rebar.
Examples of Greener Cement
Low-carbon alternatives to ordinary Portland cement (OPC) continue to proliferate. Two examples are products from CeraTech and Solidia.
Calcium metasilicate concrete
Solidia contributes two core technologies to the quest for low-carbon cement. First is the production of calcium silicate cement. Second is the use of CO2 rather than water to cure it. In 2014, Solidia concrete was first produced at Pennsylvania's Lafarge Whitehall cement plant. A NJ paver and block plant also uses Solidia concrete.
Production of Solidia’s binder occurs at lower temperatures. The chemical reaction also generates less CO2. Its patented curing process takes 24 hours instead of the standard 28 days. The product’s carbon footprint is up to 70% less than that of OPC.
In May 2022, the U.S. Department of Energy awarded Solidia $2.1 million to further develop CCUS technologies.
Calcium silicate illuminate hydrate concrete
So-called “CASH” concrete features a very dense crystalline material. It resists cracking and sulfate attacks. Corrosion resistance is three to four times that of OPC. It also demonstrates low chloride permeability. Furthermore, it exhibits early strength during the curing process. FireRok is one example. One to three days after placement, it can sustain intermittent temperatures of 1800º F. This makes it an ideal option in certain repair applications.
Green Cement: Challenges
Green cement formulations often rely on feedstocks unavailable at certain locations. Long-distance transportation utilizing fossil fuels offsets emissions reductions. Also, green cement often relies on renewable energy to meet emissions goals. Wind and solar are both localized and intermittent. And, hydroelectric energy is uncommon in certain regions.
Possibilities grow when there’s relatively cheap, renewable energy. For example, consider the 87 Mw hydrogen electrolyzer plant under construction in Varennes, Quebec. Hydro-Quebec’s 60 hydroelectric facilities generate 36.7 GW of power that’s 99% clean.
When fully operational, the plant will generate an estimated 11,000 metric tons of hydrogen and 88,000 metric tons of oxygen per year. Hydrogen is the gasification agent at the Varennes Carbon Recycling Plant. It will transform non-recyclable waste into biofuels. The plant will produce 33 million gallons of biofuels every year.
About PACA
The Pennsylvania Aggregates and Concrete Association (PACA) uses SpecifyConcrete.org to report on industry developments. Its audience is the general public as well as association members.
Our team is ready to answer your questions about your next project. Please contact us at your convenience.
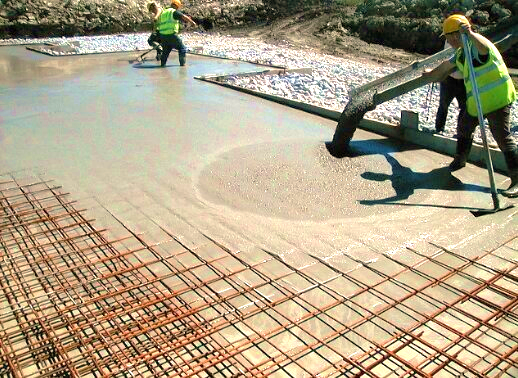