Posted on October 01, 2020
CCUS is an acronym you'll hear more about in the concrete industry. It refers to “Carbon Capture, Utilization and Storage.” The term encompasses different means used in pursuit of a singular goal, limiting the amount of carbon dioxide in the blanket of air that hugs our planet.
Humans have used concrete for shelter for more than 6,000 years. However, half of the concrete ever produced is less than 20 years old. Today, the annual worth of the global concrete industry is about $1 trillion.
Therefore, every new eco-friendly cement or concrete technology can have a large impact on global emissions. This post examines some innovative types of concrete that positively impact carbon emissions.
The concrete industry has long sought eco-friendly solutions. For example, it recycles a great deal of industrial waste. In fact, it has already used 26 million tons of industrial byproducts otherwise destined for landfills. Concrete’s role in CCUS will further expand its role in a more sustainable future.
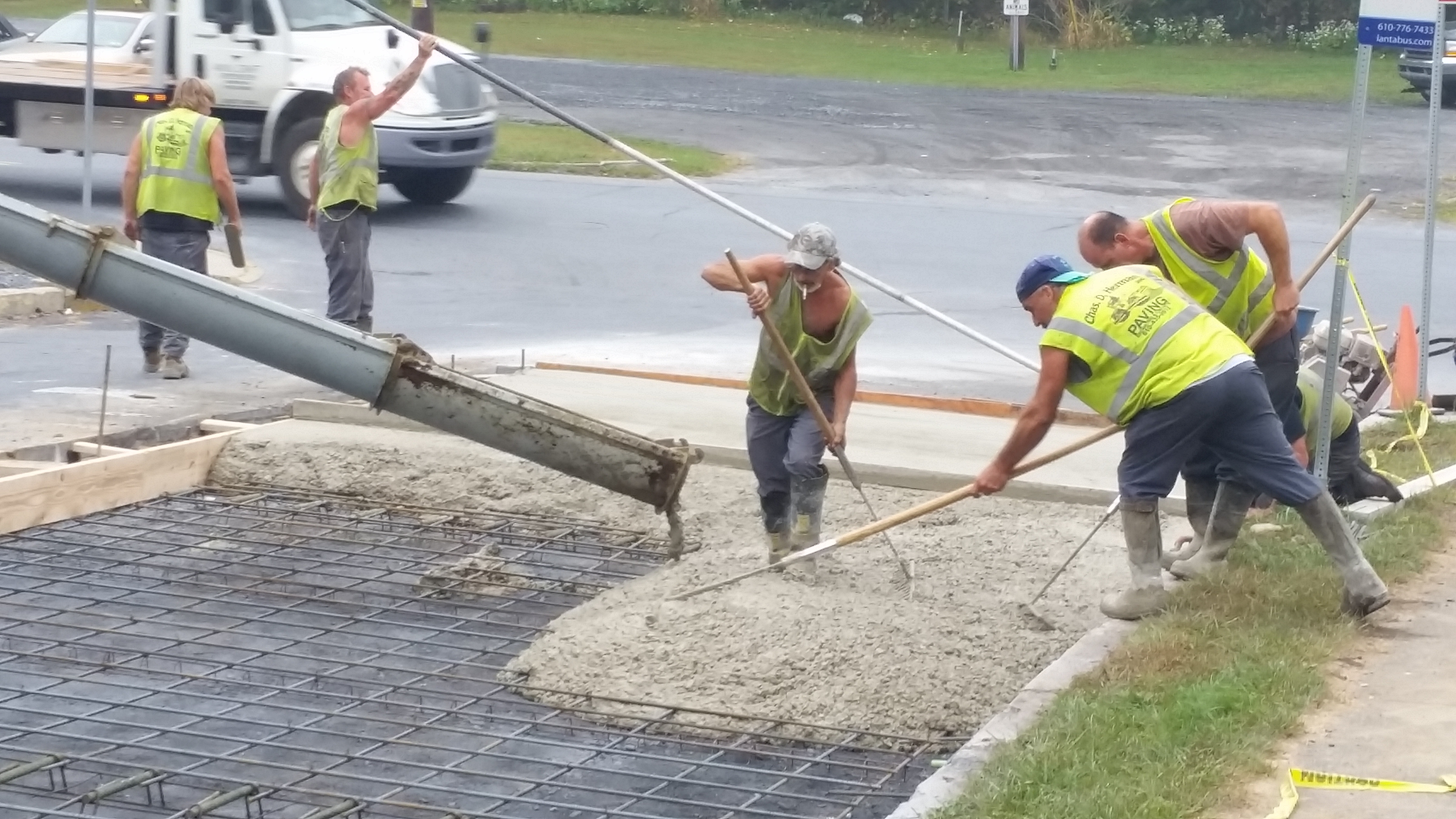
Secrets of Ancient Concrete
There are some pretty impressive concrete structures dating back more than 2,000 years. Researchers are now unlocking the secrets of ancient concrete surviving to this day. Concrete delivers the longest lifespan of any traditional building material.
Portus Cosanus is a concrete pier in Italy’s Orbetello region. Researchers at Philadelphia's Drexel University studied cores taken from the pier. The cores establish that Roman engineers fashioned concrete from volcanic ash and lime. The mixing water came from the sea. The saltwater set off a pozzolanic reaction. Crystals formed in gaps in the concrete to make the concrete stronger. The chemical reaction also stopped internal cracks from expanding. The composition of ancient Roman seawalls is similar. Their longevity derives from a mixture of lime, ash, seawater and aluminum tobermorite.
Concrete's Role in CCUS
Appropriately, the term “calcination” comes from the Latin “calcinare,” meaning “to burn lime.” During calcination in cement kilns, calcium carbonate (limestone) decomposes into calcium oxide (lime) and carbon dioxide.
During carbonation, CO2 in the air interacts with concrete's hydration elements to form carbonates. It is a slow, natural process. Carbonation gradually decreases as surfaces become less permeable. For as long as concrete has been placed, its exposed surfaces have captured carbon from the air.
Effective CO2 sequestration via carbonation depends on a number of variables:
- Surface orientation
- Surface-to-volume ratio
- Binder constituents
- Surface treatments
- Porosity
- Strength
- Temperature & humidity
Total carbonation in the world's aging concrete surfaces is quite significant. “Substantial Global Carbon Uptake by Cement Carbonation" discusses the planet’s total CO2 uptake over the last 85 years. Researchers identified the sequestering of 4.5 gigatons of CO2 in concrete during the period. This is enough to offset approximately 43 percent of carbon emissions from calcination.
Concrete & carbon capture — synthetic limestone
Roughly 50 gigatons of aggregates are used every year in concrete, asphalt and road base. Other than water, aggregates are the most transported material on the planet. Synthetic aggregates that capture CO2 are an attractive alternative to mined rock. Now, there’s a process that works around the expensive, energy-consuming process of purifying CO2.
Synthetic aggregates sequester CO2 from industrial exhaust or directly from the air. It is a very effective means of carbon capture. Every ton of synthetic limestone from California-based Blue Planet Ltd sequesters 440 kg of CO2. Its product has already been used in a project at San Francisco International Airport. Under the right circumstances, concrete using Blue Planet’s aggregates can be even better than carbon neutral.
BluePlanet’s synthetic limestone is 44 percent sequestered CO2. A cubic yard of concrete contains roughly 3,000 pounds of aggregate. This means that the carbon offset is 1320 pounds. Consider when the process is used to capture CO2 directly from a cement kiln. It’s carbon footprint shrinks by another 600 pounds, for a total of 1920 pounds per cubic yard of concrete.
Concrete & carbon utilization — cure concrete with CO2
It’s also possible to put CO2 to work in accelerating the curing process. CO2 injected into fresh concrete under low pressure mineralizes into calcium carbonate (CaCO3). This sequesters the CO2 while adding to the product’s compressive strength.
A new building on the LinkedIn campus in Mountain View, CA, will use concrete cured with CO2. This is part of an effort to reduce the company’s overall carbon emissions 75 percent by 2030. Concrete cured with CO2 decreases the building's carbon footprint by about five percent. Project managers estimate carbon savings at 240,000 pounds. This is the amount of carbon 150 acres of trees will absorb in a year.
Concrete & carbon storage — CO2 injection
CO2 injection reduces CO2 emissions in two ways. First, through the direct sequestration of CO2. Second, by reducing cement demand. For example, a company called CarbonCure captures CO2 from industrial emissions. It is purified, liquefied and injected into pressurized tanks delivered to concrete plants. There, it is injected into the concrete during the mixing process.
The injected CO2 actually enhances compressive strength. In fact, CarbonCure concrete requires less cement to achieve a specified strength. This further reduces the carbon emissions of a project. Pouring fewer cubic yards of concrete saves money. These savings offset the investment in licensing and equipment.
It's vital to further align the production of cement and concrete with the environmental needs of the planet.
Learn More
SpecifyConcrete.org is an educational website maintained by the Pennsylvania Aggregates and Concrete Association (PACA) for the benefit of its members and the public. To learn more about concrete’s role in CCUS, please contact us.