Posted on June 28, 2018
The unsurpassed quality, strength and durability of concrete make it an excellent choice for parking lot construction.
During the course of its impressive service life, a concrete parking lot requires only minimal maintenance like occasional joint sealing and cleaning. Maintenance savings accrue year after year.
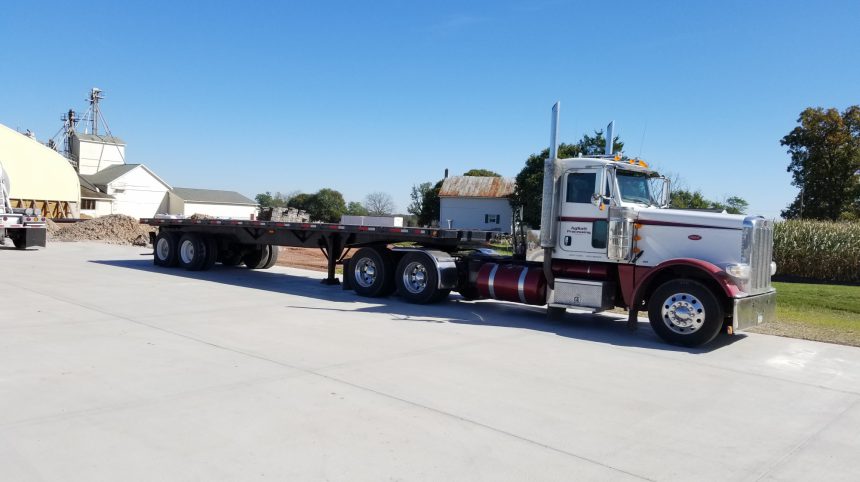
Concrete vs. Asphalt
Developers and business owners have long debated whether to pave parking lots with asphalt or concrete. The newer ACI 330 standard reduces the cost of materials associated with concrete lots. Concrete's reflectivity and long-term surface integrity are other important considerations.
Reflectivity and lighting
Light-colored concrete reflects more light than dark asphalt. This quality reduces the cost of luminaires, and it delivers energy savings year after year.
In a 2011 study, Walmart, the Department of Energy (DOE) and Pacific Northwest National Laboratory collaborated to determine the benefits of LED lighting used in conjunction with concrete pavement at a Walmart in Leavenworth, KS.
Walmart conducted exit interviews at its Leavenworth store and another of its locations in Peoria, IL. The Leavenworth lot combined concrete with 211-watt and 164-watt LED lighting, while the Peoria lot combined asphalt and 1000-watt metal halide lighting. The lesser light output of the LEDs was offset by the higher reflectivity of the concrete. Consequently, survey participants expressed satisfaction with the lighting of the concrete lot.
The LED+concrete configuration used less than half the energy required in the metal halide+asphalt configuration.
Heat island effect
The heat island effect impacts all who use asphalt parking lots. Consumer and employee satisfaction may be adversely affected by the heat radiating off the lot on hot summer days.
Asphalt absorbs the sun's UV radiation to such a degree that summertime surface temperatures may reach 140 degrees F. At this point, the surface sometimes turn soft and oily, with residue potentially accumulating on the soles of shoes.
Surface integrity
Deterioration results from ultraviolet light and moisture breaking molecular chains in the asphalt surface. Gradual surface degradation often leads to cracks which expand during freeze-thaw cycles. Dissolution of asphalt may eventually cause potholes to develop.
Asphalt requires periodic sealcoating and resurfacing, which increases life-cycle costs while potentially causing additional business interruptions.
Solubility
Concrete is non-soluble while asphalt is not. Since prolonged exposure to water may contribute to the premature deterioration of asphalt parking lots, proper drainage is a must.
Concrete Specifications for Concrete Parking Lots
New design criteria substantially reduce the costs associated with concrete parking lots. Specifically, ACI 330 revises project criteria to reduce subbase requirements. It recognizes that parking lots are different than streets and highways.
Site prep
Since asphalt flexes, the thickness and composition of base materials are important considerations. Bases must be solid enough to support the asphalt parking lot while remaining flexible enough to cope with the temperature extremes common in Pennsylvania.
Any irregularity in base materials may manifest itself in the form of cracks or sinking as asphalt expansion and contraction occur.
Material selection & thickness
The superior strength of concrete translates into reduced material requirements compared to asphalt. For example, a standard-duty lot requires a 3-inch of asphalt applied over a 10-inch subbase. Compare this to 5-inch of concrete simply poured over the compacted earth per ACI 330. For heavy-duty lots, the newer standard specifies four inches of asphalt over 12 inches of base vs. 6.5 inches of concrete applied directly over a compacted earth base.
Using traditional design methodologies, standard-duty concrete lots required 7-inch of concrete over a 6-in subbase. The newer standard specifies 5-inch of concrete with no subbase. Heavy-duty lots that were once designed with 8-inch of concrete over a 6-inch subbase now require 6-inch concrete over a 4-inch subbase.
Jointing guidelines
Slab concrete in parking lots gets harder over time. Cracking is inevitable, but it can be controlled through jointing. Proper jointing requires that any restraint is identified and located, so the location of cracking can be anticipated with a degree of precision.
The location of joints should not be left to the concrete contractor. Instead, it should be calculated by qualified personnel. Joint spacing is related to the thickness of the concrete slab. For example, control joints should be 15 feet apart on an 8-inch slab, but only 10 to 12 feet apart on a 5-inch slab.
Free Design Assistance Program
It is possible to convert your asphalt parking lot design to a concrete design at no cost to you. The Design Assistance Program is a collaborative effort by PACA and pavement engineers from the National Ready Mixed Concrete Association (NRMCA). Experts work with you to convert your asphalt parking lot specifications to concrete. The only requirement is that you use a PACA supplier a the source of the concrete.
Any 10,000 square feet or larger parking lot qualifies. Walkways, campus pathways and even patios meeting the size requirement also qualify.
The free service includes:
- A CAD drawing that includes design details like curbs, gutters, drains and thickened edges. It also includes important details like a jointing plan.
- A transmittal letter detailing recommended concrete thicknesses reflecting accepted engineering practices for expected loads. As applicable, references to NRMCA's Concrete Pavement Analyst software and ACI 330R, "Guide for Design and Construction of Concrete Parking Lots" are included.
- Base materials list
- LEED point potential
- Subgrade and drainage determinations for concrete pavements, with or without detention
- A hydrological illustration is included for pervious concrete projects
- Potential sources for specifications relevant to the parking lot project
Disclaimer: Although design suggestions do not necessarily include every known concrete fact, they do comply with current industry standards. Ultimately, the final design remains the responsibility of the project's engineer on record.
Contact Us Today
Contact PACA today for more information about this free design service. Please click here for a sample design proposal.