Posted on April 01, 2021
Since 1990, global concrete industry emissions are down 19.2 percent per ton. This is according to the Global Cement and Concrete Association. Its 2050 “Climate Ambition” seeks carbon-neutral concrete.
United States concrete production continues at high levels. According to the New York Times, “370 million cubic yards of concrete was produced last year, with nearly 40 percent of it going into commercial real estate.” There are very different ways to make concrete more sustainable. One is to reduce the energy required to produce it. The other is to rely more on renewable energy to produce it.
Industrial carbon emissions are a concern worldwide. Today, the concrete industry intensifies its focus on reducing its carbon footprint. Carbon Capture, Utilization and Storage (CCUS) is a key part of the strategy. CCUS is part of a comprehensive effort that takes on carbon emissions at every level. A September 1, 2020, GCCA statement cites key industry goals:
- Reduce process emissions via CCUS
- Address direct energy emissions
- Use renewable energy to reduce indirect energy emissions
- Take advantage of concrete’s capacity to absorb and store atmospheric CO2
The International Energy Agency (IEA) calls on stakeholders to “Establish a market for low-carbon materials, including steel and cement, through public and private procurement measures.”
When it comes to carbon dioxide, there are many ways to catch it, liquefy it, inject it, store it and otherwise use it. Simultaneously, renewable energy sources are an increasingly vital alternative to fossil fuels.
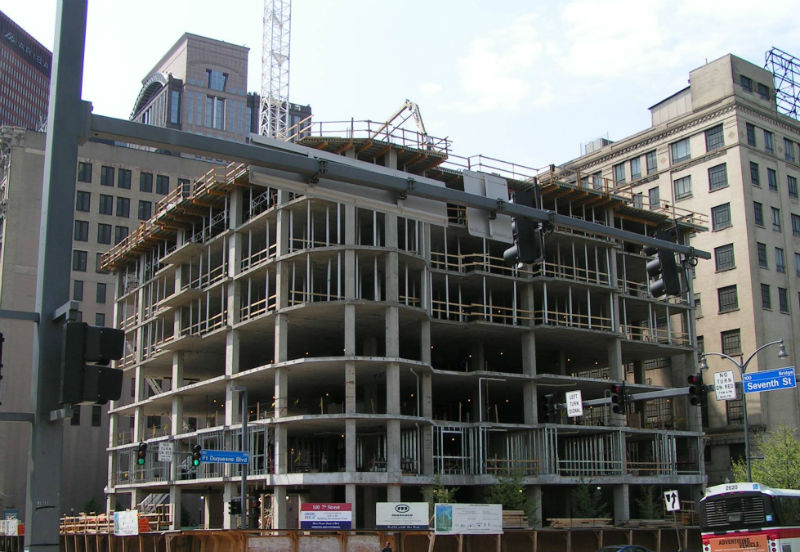
Carbon Capture amid Continuing Demand for Concrete
Cement is the binder responsible for transforming sand, gravel and water into concrete. It accounts for about five to seven percent of global CO2 emissions.
During the next four decades, the U.N. estimates construction of another 230 billion sq-m of floor area worldwide. This will equal the total floor area already in existence. Demand for concrete and sustainability are on a collision course. Carbon capture, efficient cement production and reliance on renewable energy are all vital. The continued success of the concrete industry depends on it.
Case Studies in Sustainability
The cost of new carbon capture technologies is a concern. Refinement and scalability are keys to reducing costs that make widespread adoption possible.
Cemex collaborates with Carbon Clean
Cost reduction is a key goal driving a new partnership between Cemex and Carbon Clean. According to a press release, “Carbon Clean uses an integrated modular system that works using rotating packed beds (RPBs) to intensify the carbon capture process.” This reduces space requirements while reducing costs. Cemex expects to complete an industrial-scale pilot project in Q1 2021. It will capture 100,000 tons of C02 per year at a target cost of $30 per ton or less. Carbon Clean’s stated goal is net-zero CO2 concrete by 2050.
UCLA researchers develop CO2 concrete
UCLA researchers capture CO2 from raw flue gas. They harvest it from cement plants and other industrial facilities. It is part of UCLA's mission to find innovative ways to decarbonize heavy industry.
In July, 2020, the university announced receipt of $2.9 million in grants and awards. The Department of Energy contributed $2 million of the total. A pilot project in Gillette, Wyoming, seeks to produce 140 tons of CO2 concrete during a 90-day period.
Carbon8 Systems captures CO2 in aggregates
Carbon8 Systems mixes captured C02 with cement bypass dust to produce aggregates onsite. There have been successful pilot projects in both Canada and the United Kingdom. The next step is a major commercial agreement.
Mirrors in the Mojave
The Mojave Desert is the site of a project that counts Bill Gates among the investors. An array of 400 computer-controlled mirrors focus sunlight high atop a steel tower. Working together, the mirrors act like a multi-acre magnifying glass. A small cement kiln reaches the temperatures required for clinker production.
Earlier solar thermal systems reached temperatures of up to 1050 degrees. Although this is enough to generate power, it is not high enough for industrial use. Heliogen’s closed loop system generates much higher temperatures. At 1,800 degrees, it is hot enough to create clinker nodules. As Heliogen CEO Bill Gross puts it, “Our goal is to replace and create fuel with pure, concentrated sunlight, allowing us to power the earth with the sun.” Watch a Heliogen video here.
Cement producer embraces wind power in South Dakota
In western South Dakota, cement manufacturer GCC hopes to meet half of its energy needs with wind power. It entered into a multi-year agreement with Black Hills Energy. The goal is to reduce annual CO2 emissions 50,000 metric tons per year. This is equivalent to taking 11,000 cars off the road.
Capture, liquefy and resell CO2 in Alberta
The Canadian government is providing $3 million to help fund a carbon capture feasibility study for a plant near Edmonton, AB. If the Lehigh Hanson project goes forward, it will capture 600,000 tons of carbon emissions. Instead, technicians capture, compress and liquefy the CO2. It is then resold.
Norwegians inject CO2 into the Earth
A proposed Norcem plant in Brevik, Norway, would capture up to 400,000 tons of CO2 every year. Tankers would transport liquefied CO2 far out into the North Sea. There, the plan is to inject it into the seabed at a depth exceeding 1.5 miles.
Learn More
SpecifyConcrete.org is a website of the Pennsylvania Aggregates and Concrete Association (PACA). For more information on carbon capture in the concrete industry, please contact us.