Posted on July 27, 2023
Despite an increased use of supplementary cementitious materials (SCMs), demand for Portland cement continues to grow. In the past decade alone, Portland cement production increased from 75 to 95 million metric tons in the United States.
Clinker coolers subsequently reduce temperatures to several hundred degrees. Clinker coolers:
Allow for internal heat recuperation: clinker to combustion air
Reduce clinker temperatures to facilitate clinker processing
Deliver cooling velocities that avoid adverse clinker phases and crystal size
After cooling, the clinker is ground and mixed with small amounts of gypsum and limestone. The resulting Portland cement is so fine that a single pound contains about 150 billion grains.
Heat retained during the cooling process is one measure of the efficiency of a unit. Ease of maintenance is another. Service life is also important.
Heating raw materials to such high temperatures is energy intensive. The cooling process is as well. To improve cooling efficiencies, cement plants either modify existing equipment or install new coolers. The quest for increased efficiency and reduced emissions drive decisions to invest in clinker cooler upgrades. Cooler upgrades benefit from the use of standardized parts.
Cooling Technologies
Cement plants employ a variety of cooling technologies. This is due in part to the long lifecycle of cement plants. The two main types are grate coolers and rotation coolers.
Grate coolers
A grate cooler infuses a horizontal clinker bed with cool air from below. This facilitates heat transfer from the clinker to the combustion air. Maximizing cooling velocity controls crystal size and reduces adverse clinker phases. The largest grate coolers handle more than 10,000 tons of clinker per day. Modern tech includes more sophisticated plates and enhanced forced aeration. To save energy, the trend is toward wider and fewer grates and the use of less cooling air.
Rotation coolers
Rotation coolers feature a cylinder tilted about four to seven degrees. A gear ring drive drives the cylinder. A support ring prevents it from sliding in the axial direction as clinker moves through the unit.
There are two key issues with rotation coolers. They have limited capacities, maxing out at 3,000 tons per day. Also, they are typically not compatible with modern precalciner tech.
Efficient Clinker Coolers
Claudius Peters is a global supplier of clinker coolers, equipment modifications, and components. Its 800 clinker coolers deliver capacities of anywhere from 500 to 13,000 tons of material per day.
The firm develops modern, more efficient cooling technology. It draws on its half-century of experience to inform current research. Its newer ETA cooler gets deployed with new kiln lines as well as existing equipment. It includes an HE module – a static grate in the inlet zone. The company has already performed more than 90 ETA modifications.
Designers work to tailor designs to the core machine’s environment. Customized designs typically include updates to the:
support structure
fan ducting
hydraulic piping
chloride gas bypass duct to the new clinker cooler
Design features
Typical cooling units feature horizontally arranged lanes. Updated designs raise the clinker bed to make heat exchange more effective.
A moving floor allows for clinker bed heights of more than one meter during operation. This maximizes thermal efficiency while reducing cooling air requirements. It is important to maximize the aeration area by optimizing lane widths. Cast Mulden plates reduce pressure loss, and they reduce clogging. Robust designs limit red river and clinker spillage.
ETA lane units are installed on a support structure outside the existing cooler casing. They are then pulled inside to their final position on rollers.
Case Studies: Modern Clinker Cooler Tech
Clinker cooler upgrades typically increase throughput and energy efficiency. In turn, the latter reduces emissions.
Mokra Plant in Brno, Czech Republic
The Mokra cement plant opened in 1969. The plant’s existing grate cooler was inefficient, due in part to a clinker bed height of only two feet. Higher demand for cooling air reduced thermal efficiency and increased CO2 emissions. Existing equipment was also getting more expensive to maintain. Also, the parts were increasingly hard to come by.
In 2020, the principals signed a contract for one of Claudius Peters ' 5th generation ETA coolers. It will make the pyro line more energy-efficient and therefore more sustainable.
Star Cement upgrade
Star Cement is the largest cement producer in northeast India. Engineers wanted to increase clinker production. However, they were stymied by older grate coolers that limited throughput. Excessive clinker exit temperatures also exacerbated the production bottleneck.
Management sought a quick solution that could occur during a scheduled shutdown. A CB cooler with a Wave Grate was exactly what they needed to increase production. Reduced pressure drops across the Wave Grate cut power usage while increasing cooling airflows. Specifically, the upgrade reduced clinker temps by 50ËšC. Capacity increased from 8,500 to 9,000 tons per day. The upgrade eliminated the production bottleneck.
About PACA
The Pennsylvania Aggregates and Concrete Association (PACA) reports on industry innovation on this website. This includes the ongoing quest for carbon neutrality. The team at PACA welcomes your questions about your upcoming concrete project. Please contact us for assistance!
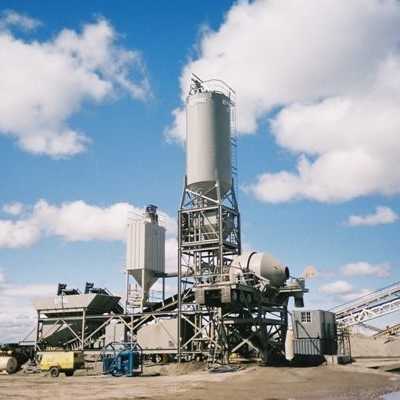