Posted on November 24, 2022
A single manufacturing process creates more than 4 billion tons of product per year. Since the process requires temperatures of 1450 degrees C, it is energy-intensive. There's another challenge as well. Calcination, the chemical reaction at the heart of the process, releases copious amounts of carbon dioxide. The product? Cement.
MIT Technology Review notes how heavy industry accounts for one-fifth of global emissions. A major part of the problem is that cement and steel production require very high temperatures. Fossil fuels generate the necessary heat, but not without significant carbon emissions.
In the cement industry, the quest for carbon neutrality requires a multi-pronged assault. It is vital to deal with the:
GHG emissions associated with generating 1450 degree C temperatures using fossil fuels
CO2 released as limestone separates into lime and CO2.
Amount of Portland cement required in concrete.
McKinsey’s analysis of the transition to net zero cement looks at myriad solutions. Green hydrogen is one of them. Heavy industry faces crucial decisions from this moment forward. Does it cast its lot with green hydrogen, or not?
The Hydrogen Fuel Alternative
Hydrogen (H2) is an abundant and highly reactive element found in water (H2O) and methane (CH4). Electrolysis splits water molecules to produce hydrogen and oxygen
2 H2O (+ electrical energy) --> 2 H2 + O2
When used as a fuel, a unit of hydrogen delivers about 2.4 times the energy as the same unit of natural gas. Hydrogen’s “emission” is water, plain and simple. No greenhouse gasses are spewed into the air. emissions. Is there a catch? Several, actually. The hydrogen must be pure. The dollar cost and the emissions cost must not be prohibitive. And, adequate supplies are a must.
An incremental approach
The partial use of green hydrogen is one way to transition to a carbon neutral future. It is possible to address supply and cost challenges over time. Combining natural gas and hydrogen is one example. Existing combustion equipment can handle a 10% hydrogen mix. Manufacturers have already designed gas turbines capable of handling higher hydrogen percentages. And, 100% hydrogen combustors are in the works.
Hydrogen production at or near cement plants
There’s good reason to consider locating electrolyzers right at cement plants. Electrolyzers yield both hydrogen and oxygen. The oxygen is also useful at the plants. Oxygen helps to:
Produce higher quality clinker
Reduce emissions
Use low-quality alternative fuels
Increase production rates
Consider a proposed system at an Austrian cement plant. It would capture CO2 and combine it with hydrogen to produce synthetic fuels. It would also yield needed plastics and chemicals.
“Reality Check: Green Hydrogen Can Scale This Decade” includes a detailed analysis by the Rocky Mountain Institute. The report suggests that, “Green hydrogen is well positioned to play a substantial role in emissions reductions by 2030. Gigawatt-scale projects are happening now, and demand is booming.”
Electrolyzer manufacturing is accelerating, and an existing infrastructure facilitates distribution. Prospects for hydrogen hubs and green shipping corridors raise expectations even further.
The Many Colors of Hydrogen Production
Hydrogen is a colorless gas. Yet, varying GHG emissions profiles get different colored labels.
Gray
At present, steam methane reformation is the most common means of hydrogen production. Producers use either natural gas or methane as the source material. Today's industrial applications mostly use hydrogen made from natural gas. But, as MIT Technology Review cautions, “the process is dirty and energy intensive.” Emissions might be as much as 20% higher than burning coal!
Brown
Brown hydrogen is a product of coal gasification. An Australian project will use brown coal to produce hydrogen. It will be liquefied for transport to Japan. Brown hydrogen becomes “blue” if CO2 capture occurs.
Blue
Blue hydrogen is a product of steam reforming. The process employs steam to separate hydrogen from natural gas. However, blue hydrogen requires capturing CO2 before it escapes into the atmosphere.
Green
Green hydrogen is the gold standard. The extraction process yields zero GHG emissions. Electrolyzers convert water into hydrogen and oxygen. The electricity required to power the electrolyzers must come from renewable sources. At present, both the cost and supply of electrolyzers limits scalability.
Another option is biomass reforming via electrocatalysis. There are two advantages. First, pre-conditioned biomass is a low cost raw material. Second, electrocatalytic hydrogen extraction is easier than water electrolysis. Another advantage is that it yields organic byproducts useful as precursors in plastics fabrication.
In the cement industry, a dream scenario is to use green hydrogen to fuel cement kilns. While cost remains a roadblock, PwC predicts a 50% decrease in hydrogen production costs by 2030.
Additional colors of hydrogen
There are still more color references. Pyrolysis breaks down natural gas into “turquoise hydrogen” and carbon. It is a zero emissions process. However, some emissions still occur during natural gas extraction and transport. “Yellow hydrogen” is a product of direct water splitting. Nuclear energy can produce “Purple hydrogen." It is also called pink or red hydrogen.
Breakthroughs in Green Hydrogen
Evidence is mounting that an era of green hydrogen is on the horizon. In fact, green hydrogen was one of MIT’s “10 Breakthrough Technologies” for 2021. Also, Green Car Reports explores the viability of scaling green hydrogen production by 2030.
At present, green hydrogen for cement kilns and other applications is just too pricey. Water electrolysis is very energy-intensive. Cheaper electrolyzers and higher capacity plants will enhance viability. The Department of Energy’s Energy Earthshots Initiative seeks an 80% decrease in the cost of green hydrogen. There is the possibility of green hydrogen costing $1 per kilogram by 2030.
Green Hydrogen to Fuel Cement Kilns
Market demand for decarbonization of heavy industry will drive demand for green hydrogen. RMI believes in the rapid scalability of green hydrogen. It notes that green hydrogen production relies on commercially mature technologies.
Net-zero kilns do not require pure green hydrogen. For example, Hanson UK’s Ribblesdale plant has a demo kiln burning a mix of 39% gray hydrogen, 12% meat and bone meal, and 49% glycerine. Substituting green hydrogen for gray delivers net zero status. A full conversion at Ribblesdale would cut 180,000 tons of CO2 emissions per year.
Future possibilities
One dream is a global array of electrolysis plants running on low-cost renewable energy. The future may also deliver new technologies for producing hydrogen. For example, New Atlas describes a process for extracting hydrogen from the air. Australian researchers have invented a Direct Air Electrolyzer (DAE) capable of extracting moisture from the air even when humidity is as low as 4%.
About PACA
The Pennsylvania Aggregates and Concrete Association (PACA) informs its members and the general public abreast of industry developments. Our staff welcomes questions about your upcoming concrete project. Please contact us at your convenience.
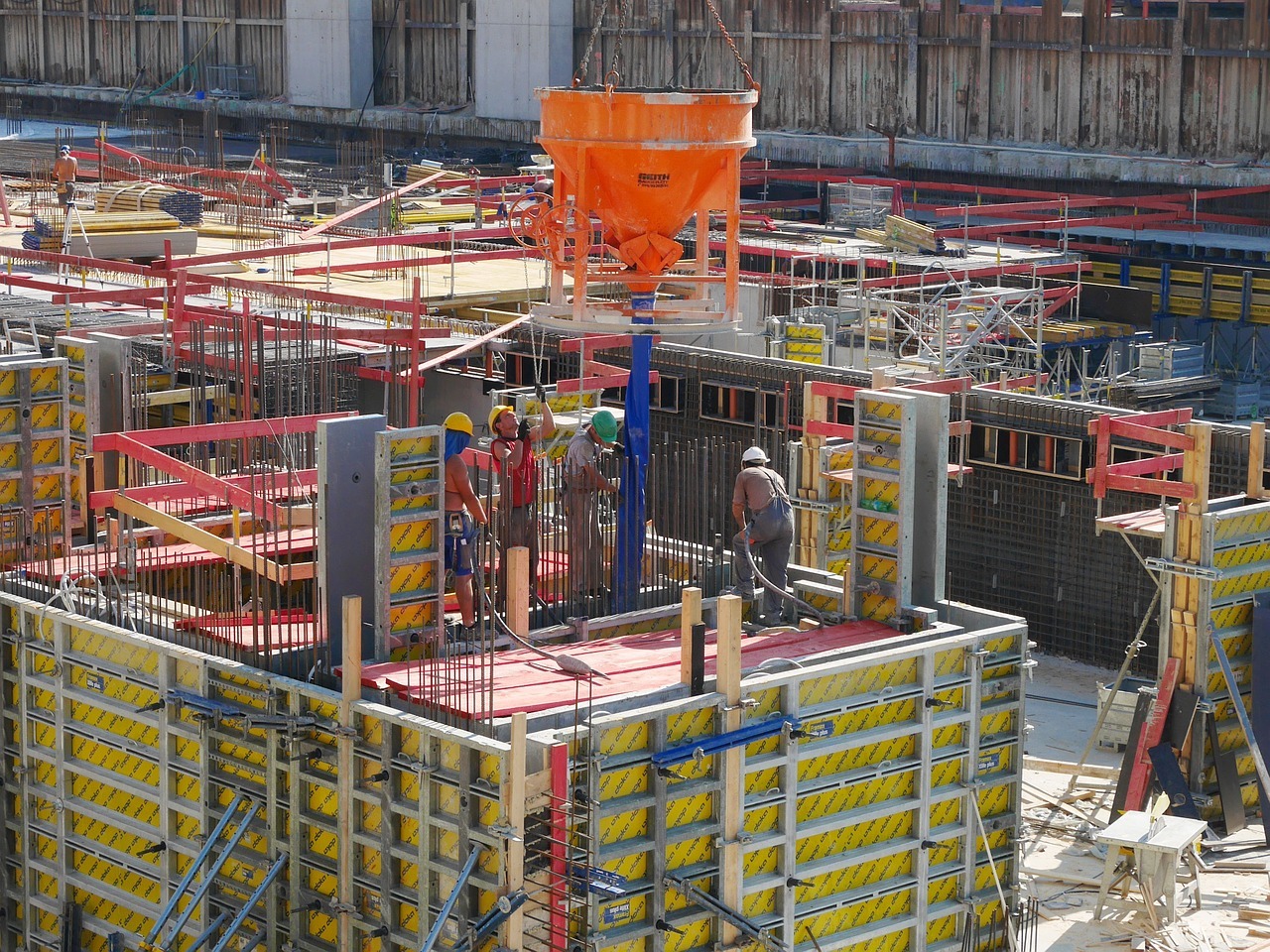