Posted on August 25, 2022
3D printed concrete (3DPC) construction offers a variety of benefits. Among them are design freedom, speedy construction, lower labor costs, and reduced waste.
This unique type of concrete construction is also fire, water and earthquake-resistant. Recent research confirms that ultra-high performance 3DPC increases the fire safety of buildings. 3D printing’s capacity to fabricate complex shapes enhances aesthetics. At the same time, it is straightforward to leave openings for windows and doors while also leaving channels for wiring and plumbing.
The era of owner-occupied 3DPC homes began several years ago. In 2018, a family moved into their 4-bedroom 3D printed home in Nantes, France. Each wall consisted of two layers of polyurethane foam with a space between for the concrete. The concrete “frame” of the residence took 54 hours to “print.” Contractors spent an additional four months adding windows, doors, and other finishing touches. Using 3DPC saved an estimated 20% over conventional wood-frame construction.
Recent History of 3D Concrete Printing
Why is 3DPC gaining acceptance for both residential and commercial projects? First off, the equipment continues to improve. Bigger gantries make larger structures possible. There are now multi-story 3DPC structures. A 6,900 sq ft municipal building in Dubai is 31-ft tall.
Various concrete mixes have been deployed in 3DPC projects. Concrete mixes featuring ordinary Portland cement (OPC) require reduced water-cement ratios. Other materials are possible. Examples include castable clay, synthetic polymers, recycled plastic and even wood flour.
Successful 3DPC requires continual layering capable of dimensional accuracy. A reliable drying factor is a must. Expert onsite monitoring considers variables like changes in ambient temperature and humidity.
Leading 3DPC Printers
For many contractors wanting to expand into 3DPC, equipment cost remains an obstacle. Systems run from less than $200k to more than $1 million. The gantry-style systems tend to be less expensive than the robotic arm systems. Some contractors deploy multiple printers to speed up the process even more.
ICON’s Vulcan printer and COBOD’s BOD2 printer currently print many of the world's most recent 3D printed structures.
ICON Vulcan 3D Printer – Texas
ICON’s next-generation Vulcan 3D is capable of producing highly resilient single-story structures. The Vulcan has printed homes up to 3,000 sq ft in size. ICON has delivered more than two dozen homes in the United States and Mexico. Investors have taken notice. In February 2022, TechCrunch reported another $185 million in funding. Total invested capital now stands at $451 million. Valuations are approaching $2 billion.
The Vulcan printer uses ICON's proprietary Lavacrete blends when printing at speeds of five to 10 inches per second. The maximum width of a structure is 36.5 feet, while the maximum height is 10.5 feet. There is no limit on length. Magma is ICON’s automated end-to-end material delivery system. It takes the guesswork out of the customized mixing of cementitious material. Adjustments occur for varying weather conditions.
ICON’s tablet-based operating system features a simple, intuitive interface. Its software converts floor plans into print jobs. It directs the Vulcan printer and the Magma mixing system. It processes real-time data to deliver quality printed structures. Powerful CAD and print planning benefit from machine learning and predictive analytics.
COBOD BOD 2 3D Printer – Denmark
COBOD counts both GE and Cemex among its investors. The COBOD BOD 2 is now one of the world’s most popular 3D concrete printers. COBOD has delivered more than 50 3DPC systems thus far. They are now available on six continents. The COBOD Configurator allows contractors to design their own BOD 2 printers.
The standard nozzle lays down a bead of concrete about two inches wide and Âľ inch thick. The BOD 2 operates at up to 196 feet per hour. Using 2.5-meter modules, it is possible to extend the gantry along any of the three axes.
Companies Building 3D Printed Homes
Long Island’s SQ4D unveiled its Autonomous Robotic Construction System (ARCS) in 2018. It uses high compression concrete with rebar reinforcement. See one of their homes under construction here. Printed Farms is a Florida-based company using a COBOD printer. It hopes their equipment will be an asset in a hurricane’s aftermath.
Emergent 3D is a U.S.-based startup with a COBOD printer. It has contracted to 3D print a church in California in 2022. We Print Homes is a joint project of homebuilder Sunconomy and Forge New. It also uses COBOD printers. It hopes to license a system to contractors.
Building a 3DPC Structure
Proponents of 3DPC cite key benefits. They include design freedom, speed, simplified construction, and resilience.
Speed
Speedy construction is often cited as a key advantage of the 3DPC process. For example, New York’s SQ4D states that it can print a 1,900 sq ft home in less than 48 hours.
Simplified construction
3DPC reduces the inefficiencies and losses associated with more traditional construction. It is possible to avoid cladding on exterior and/or interior surfaces.
Reinforcement
The 3DPC advocates continue to experiment with various types of reinforcement. They range from rebar to meshes, and from fibers to cables. Recent research establishes the pluses of 3DPC reinforced with steel fibers.
Insulation
Batiprint3D uses a robotic printer to first print polyurethane foam formwork. The same poly-articulated robot then places the concrete. The end result bears similarities to insulated concrete form (ICF) construction.
About PACA
The Pennsylvania Aggregates and Concrete Association (PACA) uses SpecifyConcrete.org to inform readers of industry innovation.
For help with your next concrete project, please contact us.
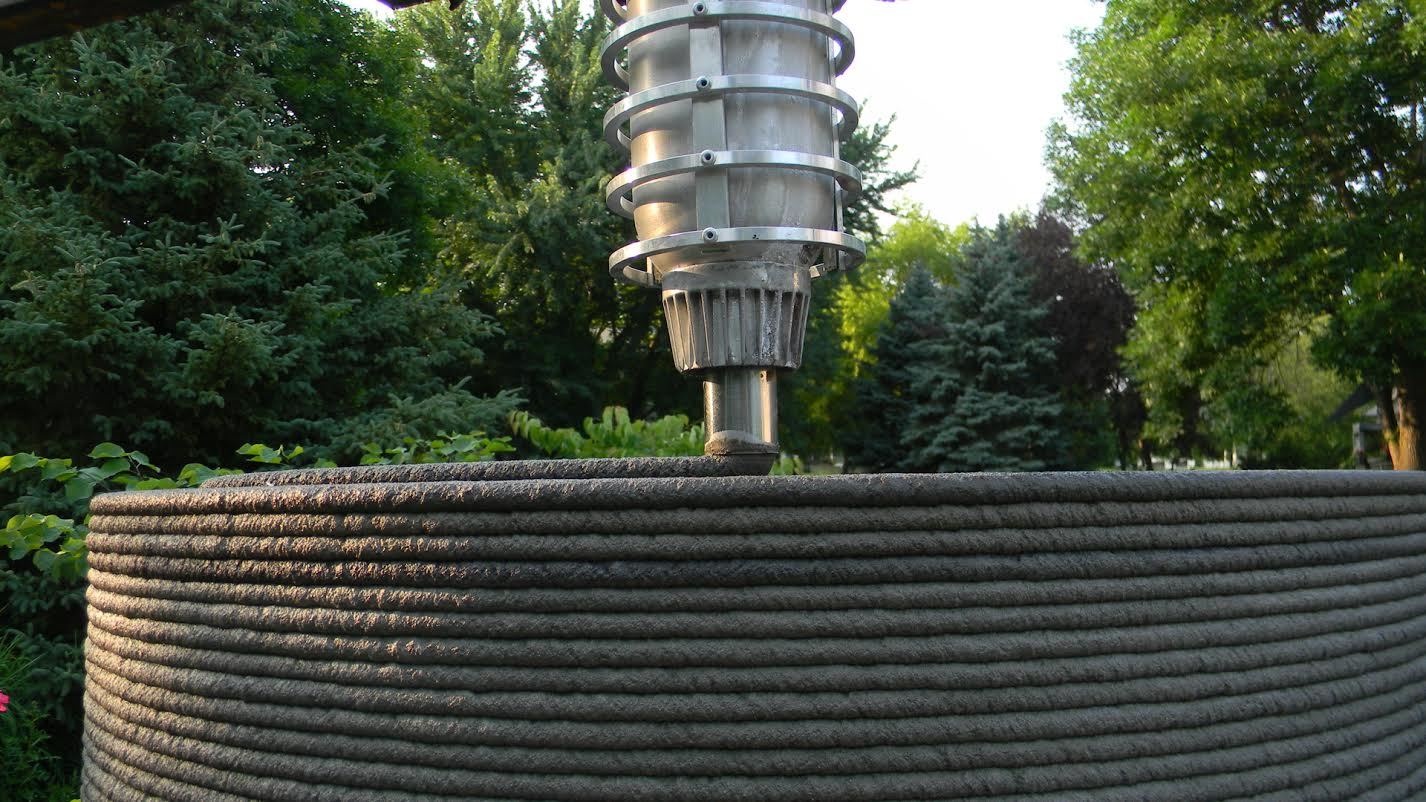